Manufacturing
In-house 3D printing facilitate the production of end-use high precision tools, jigs and fixtures for your factory floor, reducing downtime and increasing production efficiency.BCN3D Printers in Manufacturing

IDEX technology: Same investment, double productivity
IDEX technology is the only extrusion system capable of printing with two heads independently. This system allows enabling Duplication and Mirror printing modes capable of printing two pieces at a time. Double printing capacity means double productivity, all with the same investment. Unlike any other dual extrusion machines on the market, when you acquire a Sigma or Sigmax machine, you get one printer but you double your productivity. All thanks to the IDEX technology.
Big volume with the biggest printing surface
The BCN3D Epsilon offers a large print volume of 420x300x400mm. The main advantage of this feature is its proportions, offering the largest printing surface on the market with an incredible height of 400mm. This allows to print the vast majority of parts that are manufactured.
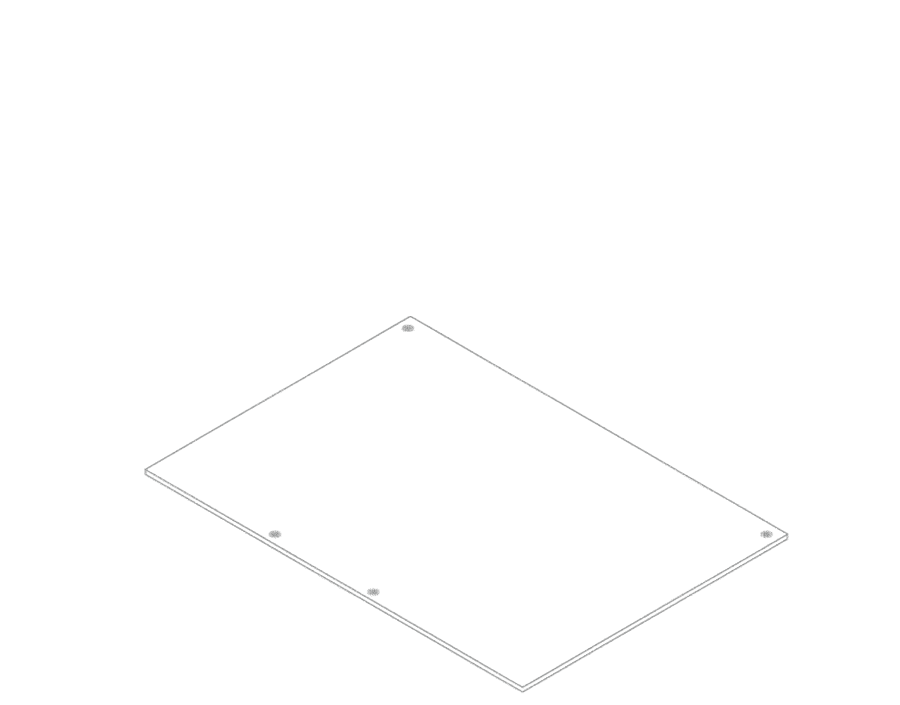
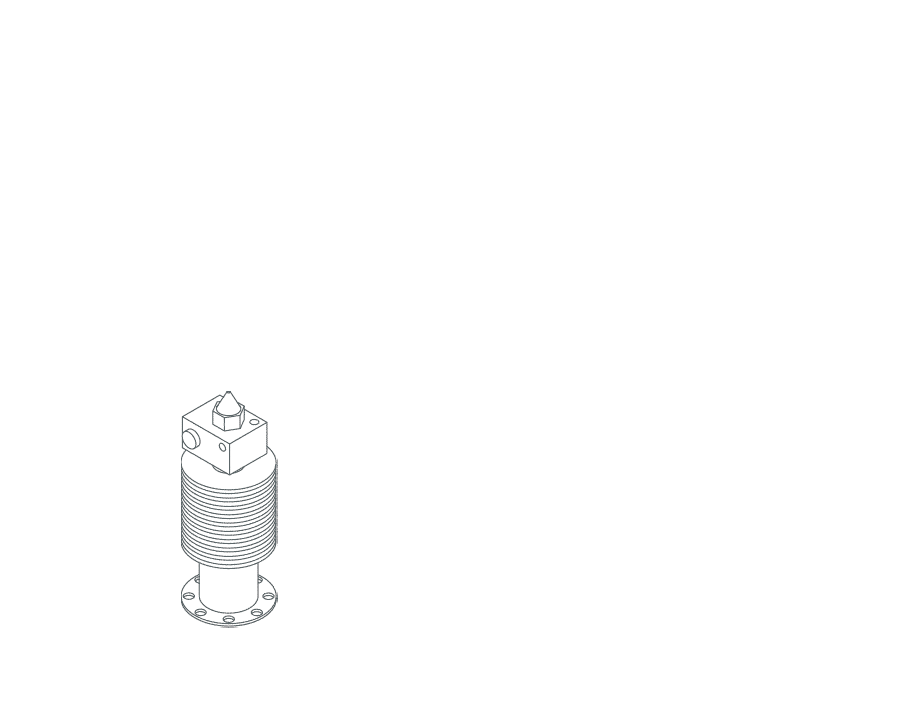
A family of hotends which adapts to your production needs
The hotend family offers a wide range of nozzle sizes that adapt to various needs; from printing small delicate details to big and robust parts. Just changing the toolhead, you will be able to manufacture the majority of the models.
Use cases in Manufacturing Industry
Precision Grinding and Erosion Leader Vollmer of America Innovates with Specialized, Cost-Effective 3D Printed Tooling
Vollmer of America, a leader in precision grinding and erosion machines, has transformed its operations by integrating additive manufacturing technology using BCN3D Epsilon printers. This has allowed the Pittsburgh-based company to swiftly create custom tools and prototypes, effectively addressing challenges such as developing specialized tools for service engineers and designing protective holders for expensive grinding wheels in smart cabinets.
Learn more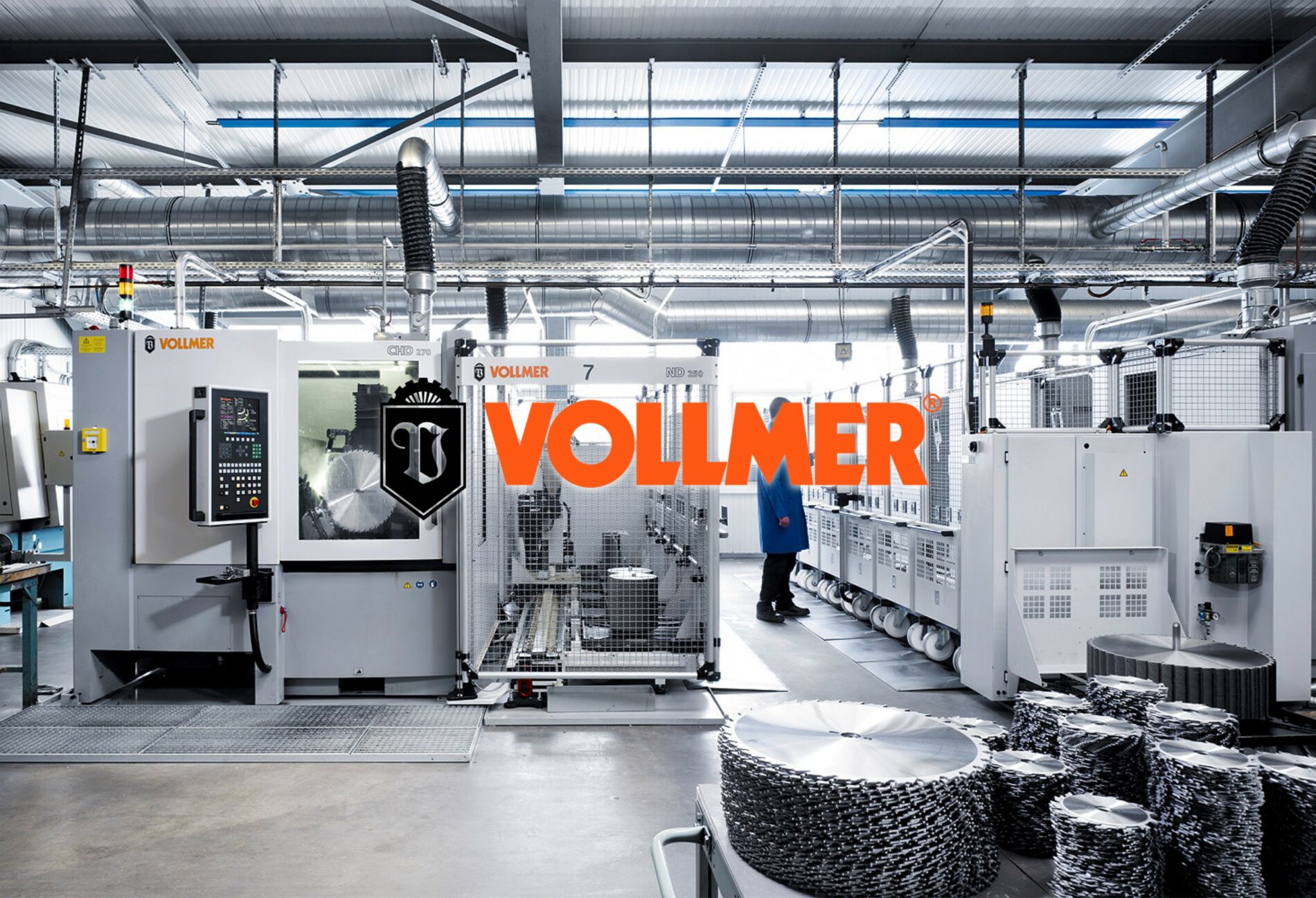

In-house 3D printed tooling brings an efficiency overhaul to Saint-Gobain’s production line
We visited industry-leading manufacturer Saint-Gobain in its facilities in L’Arboç, Barcelona. Since 2019, the incorporation of 3D printing across its shop floor has saved the company around 170.000€ and reduced lead times of its tooling by 93%. The 3D printed parts take the shape of tools, jigs, and fixtures and perform applications for anything from positioning to quality control.
Learn moreIterative design with 3D printing gives TwoNav’s GPS devices steadfast reliability
Outdoor equipment manufacturer TwoNav is experiencing a more flexible, iterative design process, a quicker time to market, and a reduction in expenses since incorporating 3D printing. The company is not only using BCN3D’s technology for designing, prototyping, and end-use parts, but also for tooling in and around their production line.
Learn more
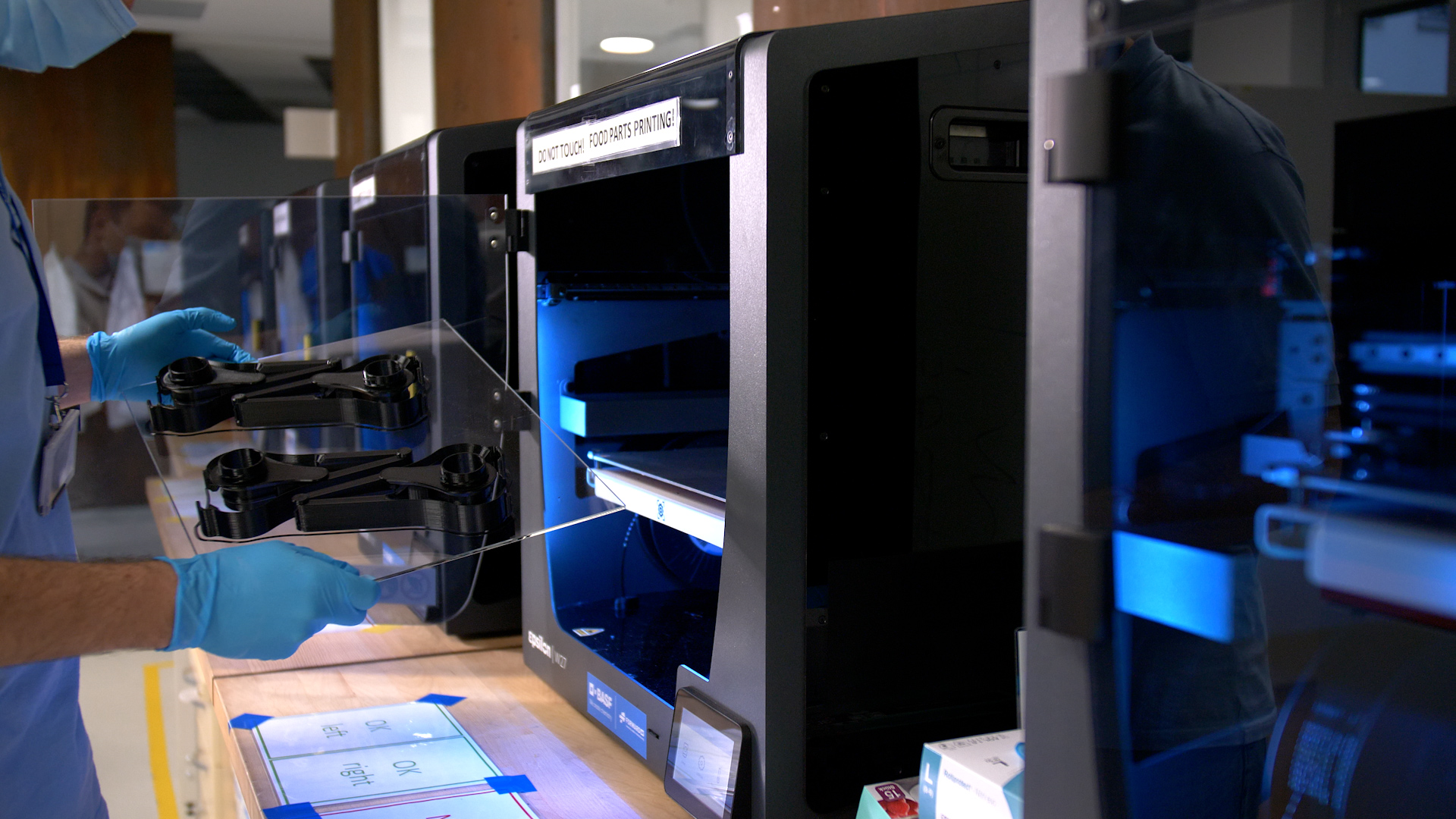
Replique and BASF Forward AM’s food safe 3D printing process for Miele
German 3D printing platform Replique and BASF Forward AM’s material experts are working together to create parts for home appliances manufacturer Miele, using a food safe 3D printing process for parts in contact with consumable goods. IDEX technology ensured a fast-tracked, profitable process for this low volume batch production.
Learn moreNissan is ahead of the curve with a dynamic implementation of 3D printed tools, jigs and fixtures in its assembly lines
Automotive giant Nissan is relying on a small farm of BCN3D printers in its Barcelona factory to fabricate 700 tools, jigs, and fixtures in its car assembly lines so far. We developed a digital library for you to see the specifications of each part. On a tour of their facilities, Trim & Chassis Manufacturing Kaizen Engineer Enric Ridao and Manager of Maintenance & Engineering Facilities Carlos Rellán told us all about their immense savings in time and costs: reducing one week to one day, and costs to 20 times less.
Learn more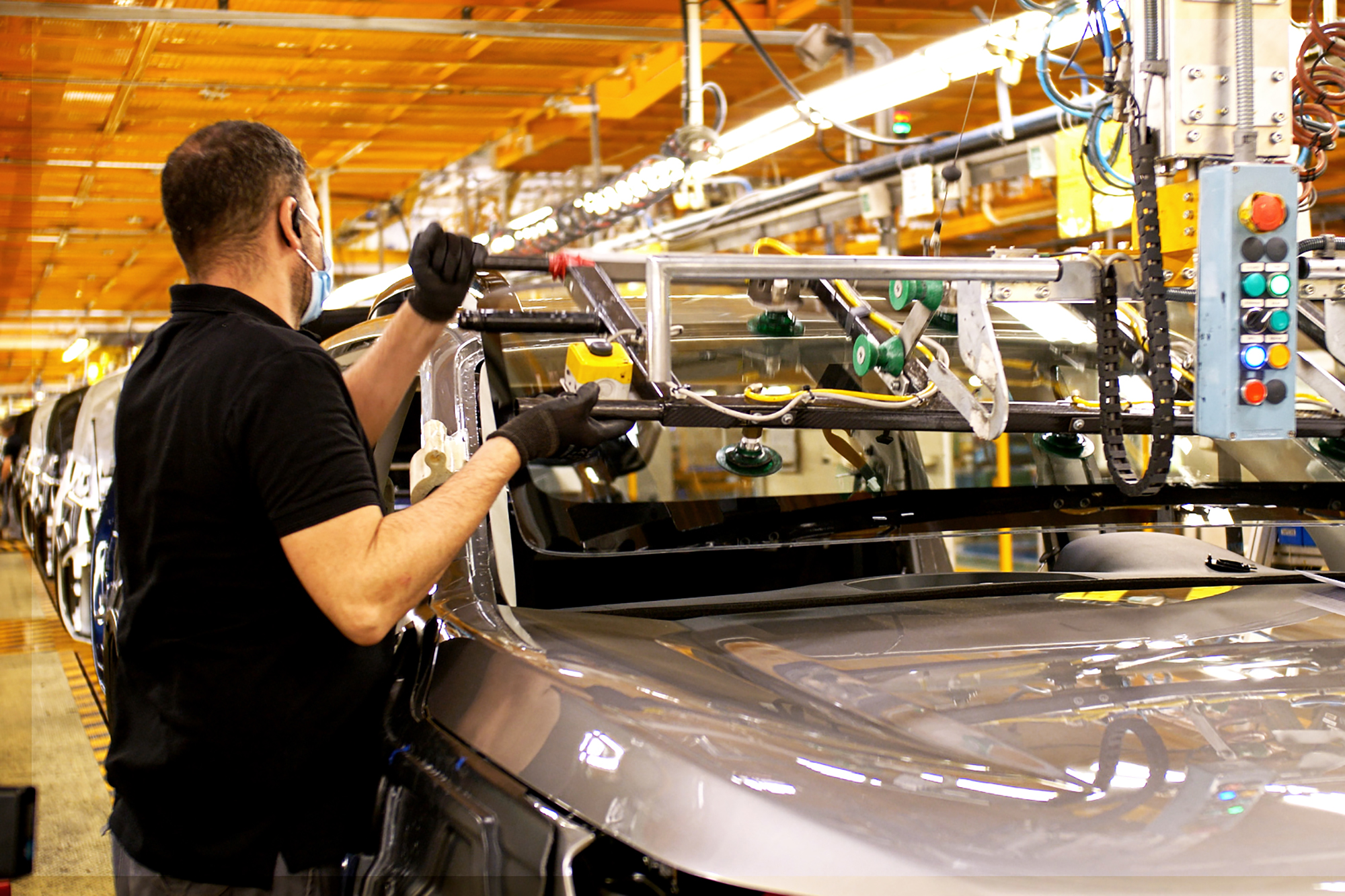
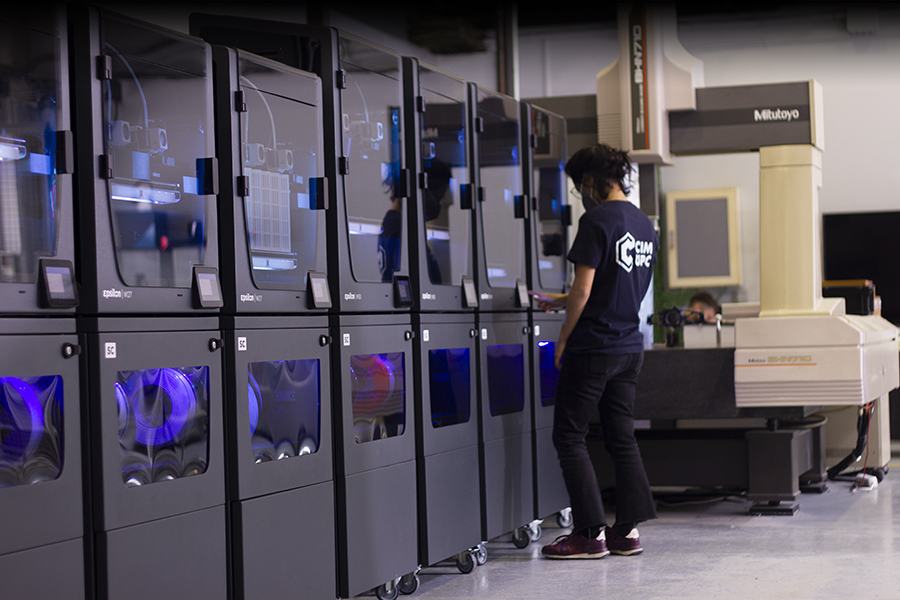
The CIM UPC step up their game with an army of BCN3D printers and Smart Cabinets
With the implementation of a small print farm of BCN3D printers and Smart Cabinets, the CIM UPC has accomplished a radical transformation of the way they produce end-use applications. Experts in the field of additive manufacturing technologies, the CIM UPC team have found the Epsilon series printers with Smart Cabinet to be the most valuable solution for both low-volume batch production and big parts.
Learn moreTecalum Industrial: Remarkable time and cost savings in the industrial sector thanks to 3D printed tooling
For Tecalum Industrial, implementing 3D printing into their day-to-day activities resulted in a great return on investment. Not only they significantly reduced the cost of producing customized tooling, jigs, and fixtures but they also save a remarkable amount of time by fabricating these parts in-house.
Learn more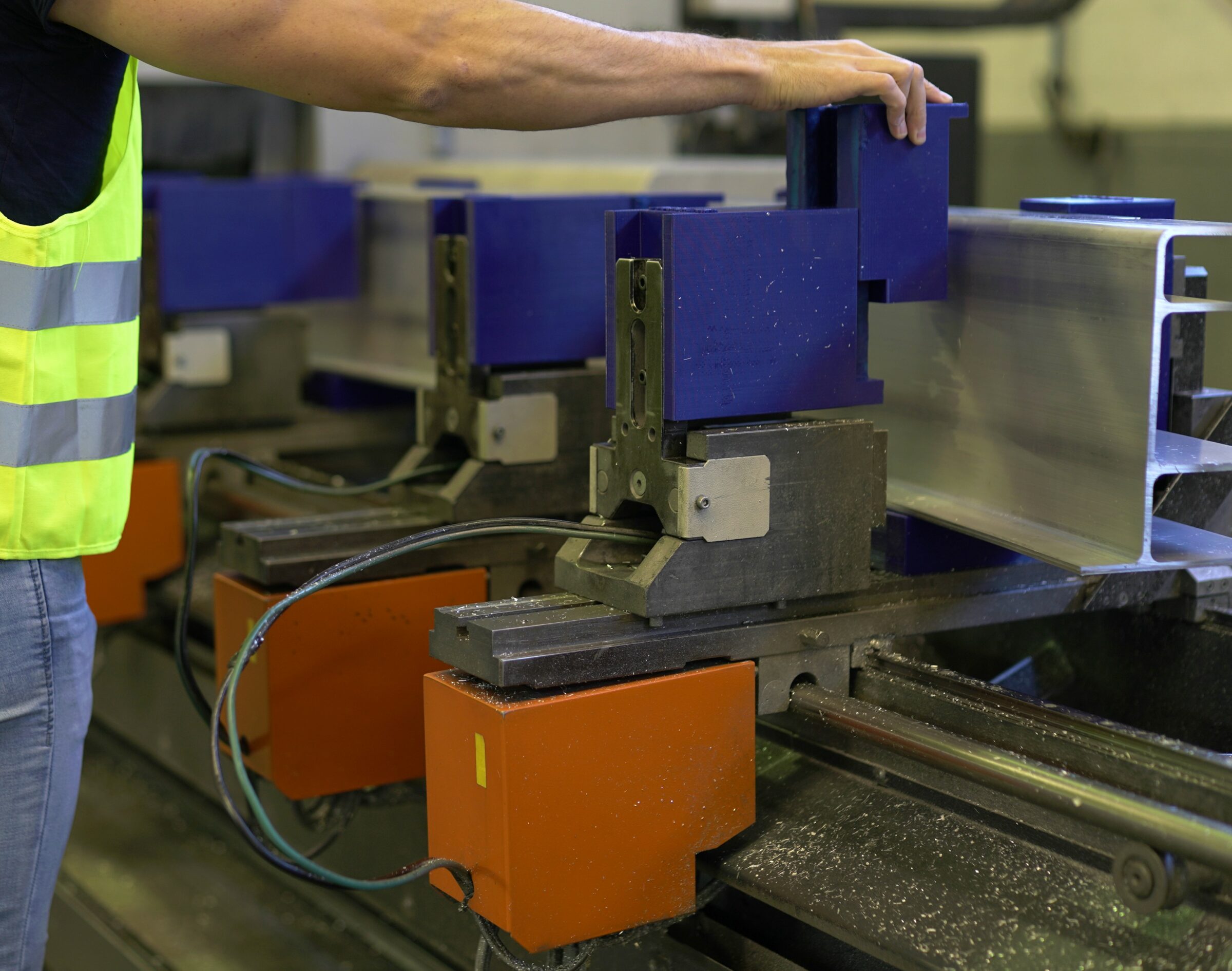
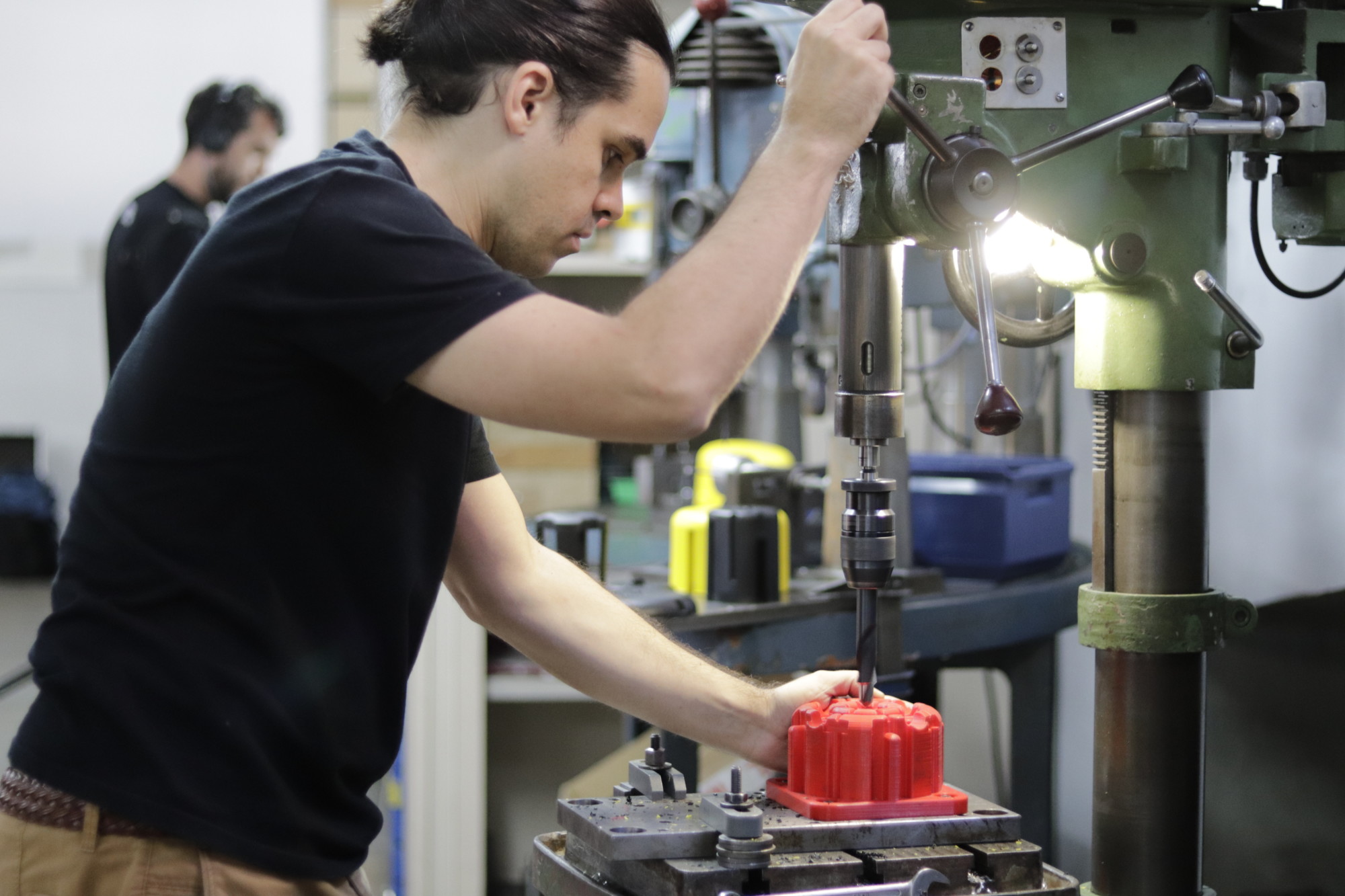
Dlimit: achieving maximum efficiency thanks to 3D printed tooling
Dlimit has revolutionized its workflow since incorporating 3D printing to fabricate 100% functional customized tooling, which enables them to maximize efficiency, reducing a significant amount of time and costs in their production process of queue management systems.
Learn moreBORN Motor: 3D printed motorcycle parts for time and cost savings
BORN Motor customizes high-quality deconstructed motorcycles and is using 3D printing for manufacturing final parts instead of traditional processes, saving €2,000 for each motorcycle modified.
Learn more
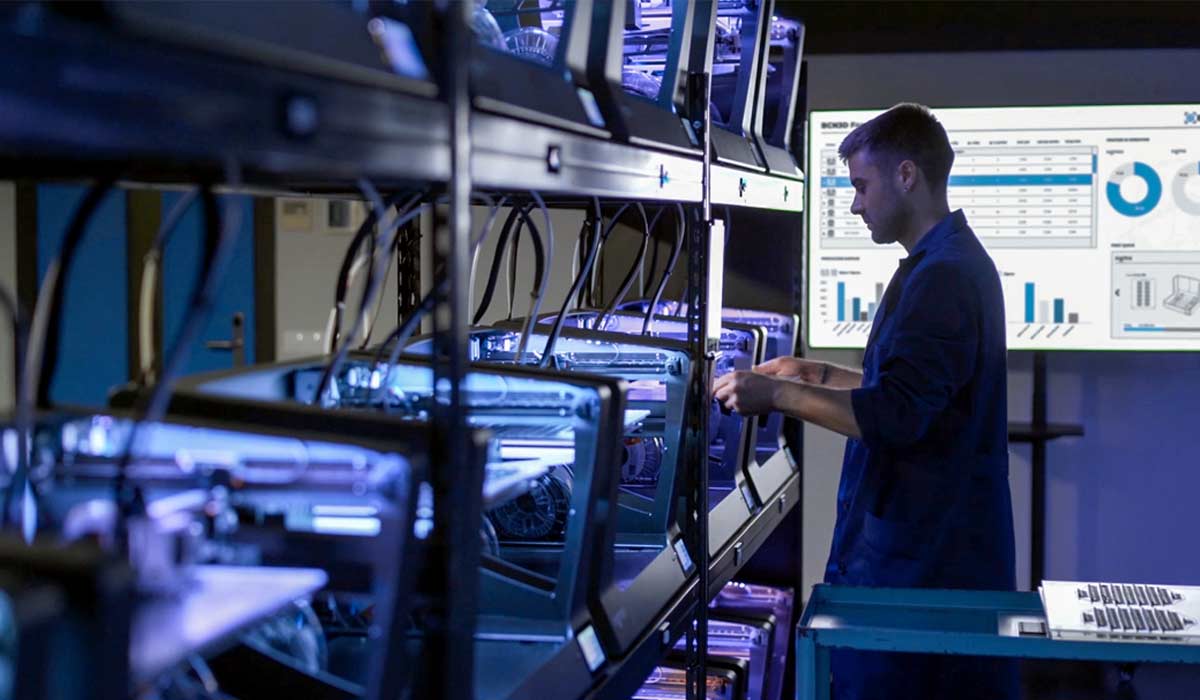
IDEX Technology for low volume batch production: Doubling productivity at the BCN3D Print Farm
BCN3D has proven that additive manufacturing is the most cost-effective solution for producing low volume batches, including 47 3D printed plastic pieces in each manufactured 3D printer.
Learn more