Product design
In-house desktop 3D printing allows product designers to turn their ideas into physical models and get feedback in only a matter of hours, making product development far more efficient.BCN3D Printers in Product design

Reliable dual extrusion 3D printing with IDEX technology
IDEX architecture is the most reliable and neat solution on the market when it comes to dual extrusion technology. This is because the two extruders work independently when printing water-soluble supports or multi-material parts. While one extruder is printing the second one is parked, preventing the drip of molten plastic into the part. Conventional dual extrusion printers have both extruders together, which may result in filament threads left on the piece.
Big volume with the biggest printing surface
The BCN3D Epsilon offers a large print volume of 420x300x400mm. The main advantage of this feature is its proportions, offering the largest printing surface on the market with an incredible height of 400mm. This allows to print the vast majority of parts that are manufactured.
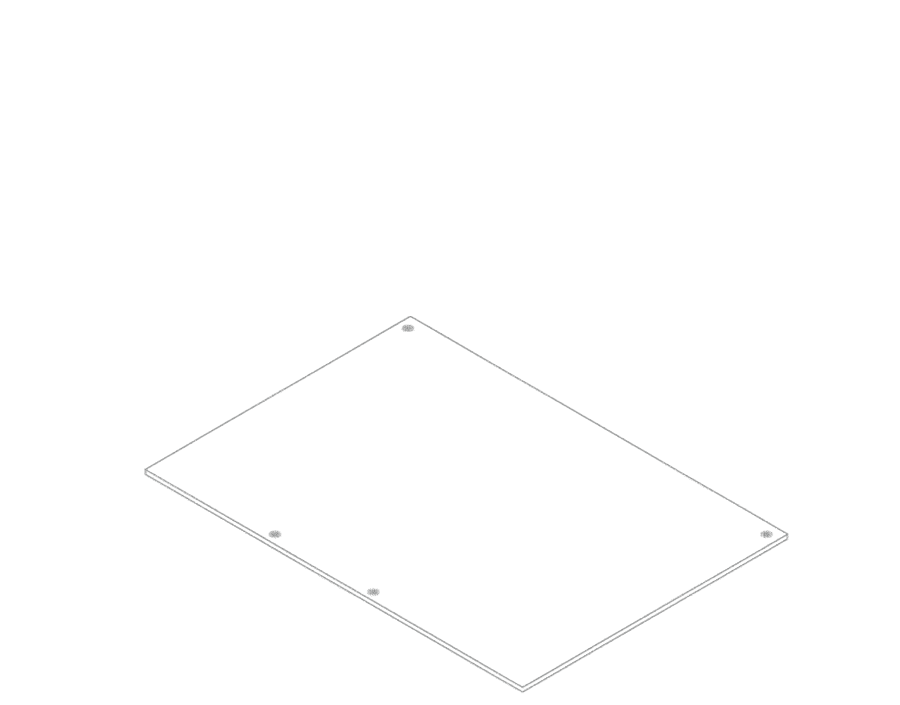

High-performance materials for professional prototyping
BCN3D Filaments are manufactured by BASF and Mitsubishi Chemical, two of the most renowned chemical corporations in the world. Their reputation in the manipulation and production of plastic materials, along with the advanced plastic processing techniques, allows BCN3D to provide the filaments with more repeatability of the market. Each spool will consistently show the same quality and will always offer the same results.
Use cases in Product Design Industry
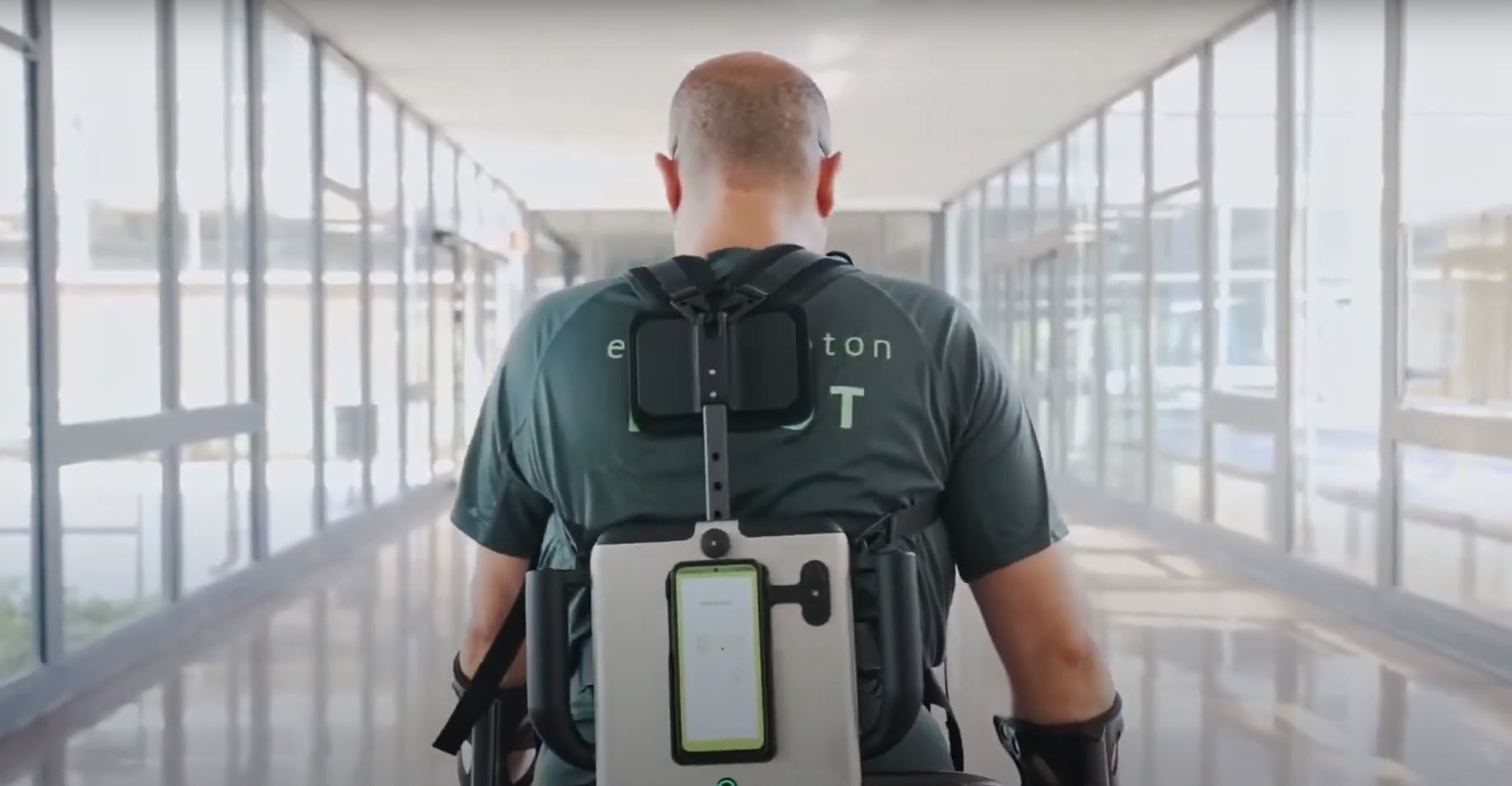
3D Printing boosts ABLE Human Motion’s exoskeletons design workflow, by improving rapid functional validation and prototyping.
At ABLE Human Motion, they believe the best way to design compelling and really useful exoskeleton technology is by involving the final users from the beginning. This implies fast design iterations incorporating the patient’s feedback, and this is where 3D printing excels.
Learn MoreIterative design with 3D printing gives TwoNav’s GPS devices steadfast reliability
Outdoor equipment manufacturer TwoNav is experiencing a more flexible, iterative design process, a quicker time to market, and a reduction in expenses since incorporating 3D printing. The company is not only using BCN3D’s technology for designing, prototyping, and end-use parts, but also for tooling in and around their production line.
Learn more
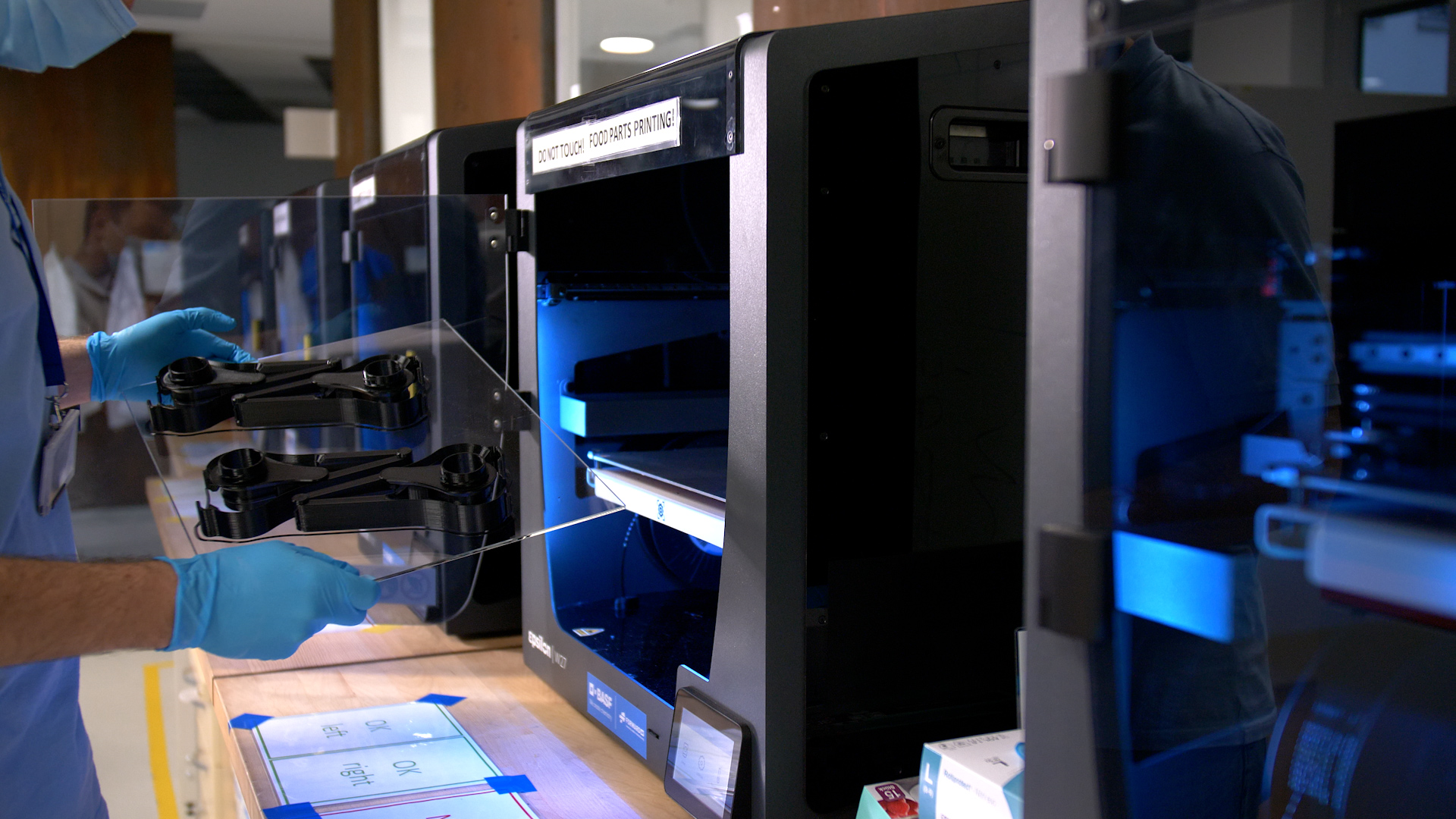
Replique and BASF Forward AM’s food safe 3D printing process for Miele
German 3D printing platform Replique and BASF Forward AM’s material experts are working together to create parts for home appliances manufacturer Miele, using a food safe 3D printing process for parts in contact with consumable goods. IDEX technology ensured a fast-tracked, profitable process for this low volume batch production.
Learn moreYuugn lights the way to a sustainable future with 3D printed light fixtures
Dutch company Yuugn creates 3D printed light fixtures for office buildings, commercial spaces, and schools while putting a focus on sustainability.
Learn more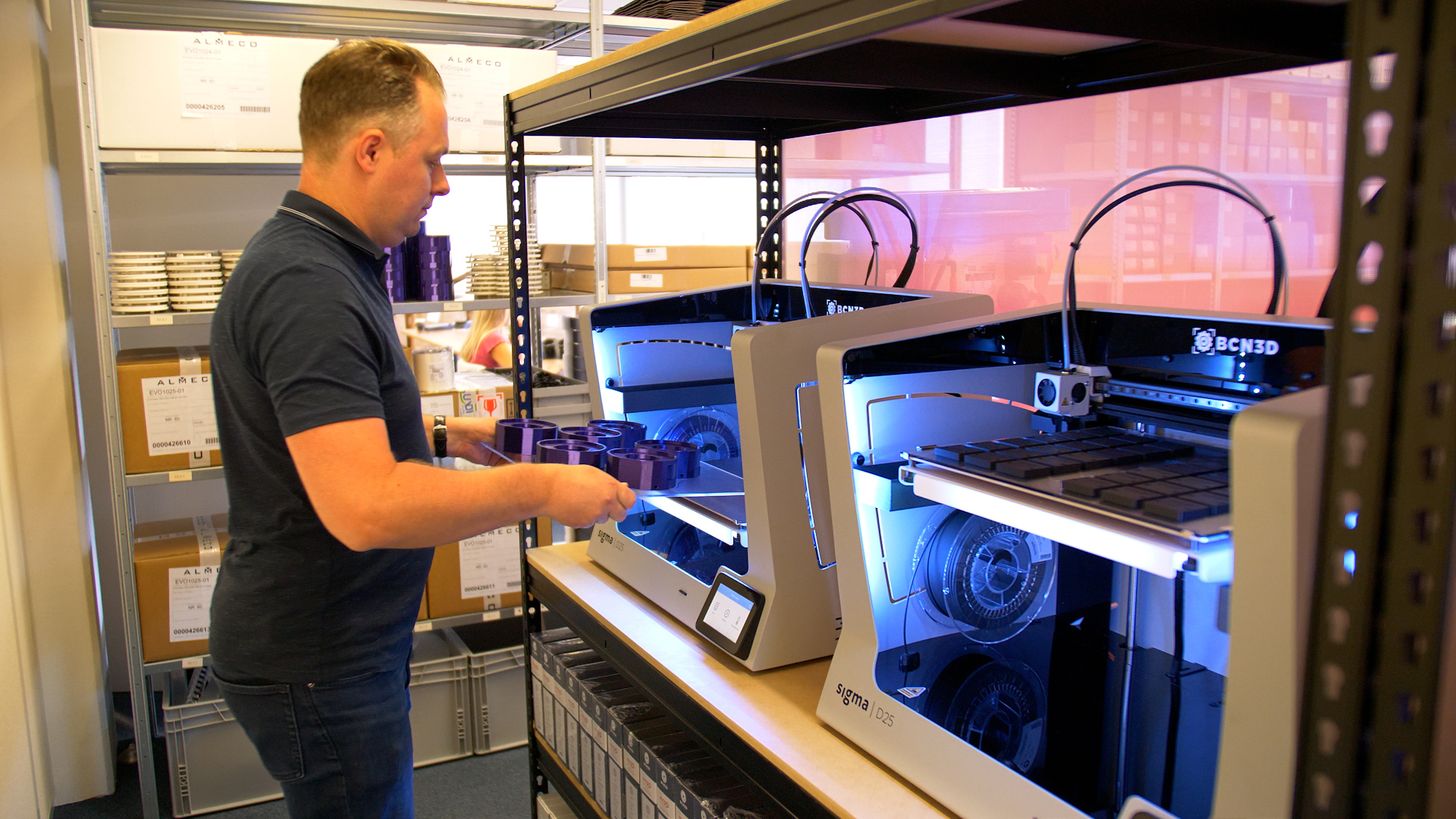
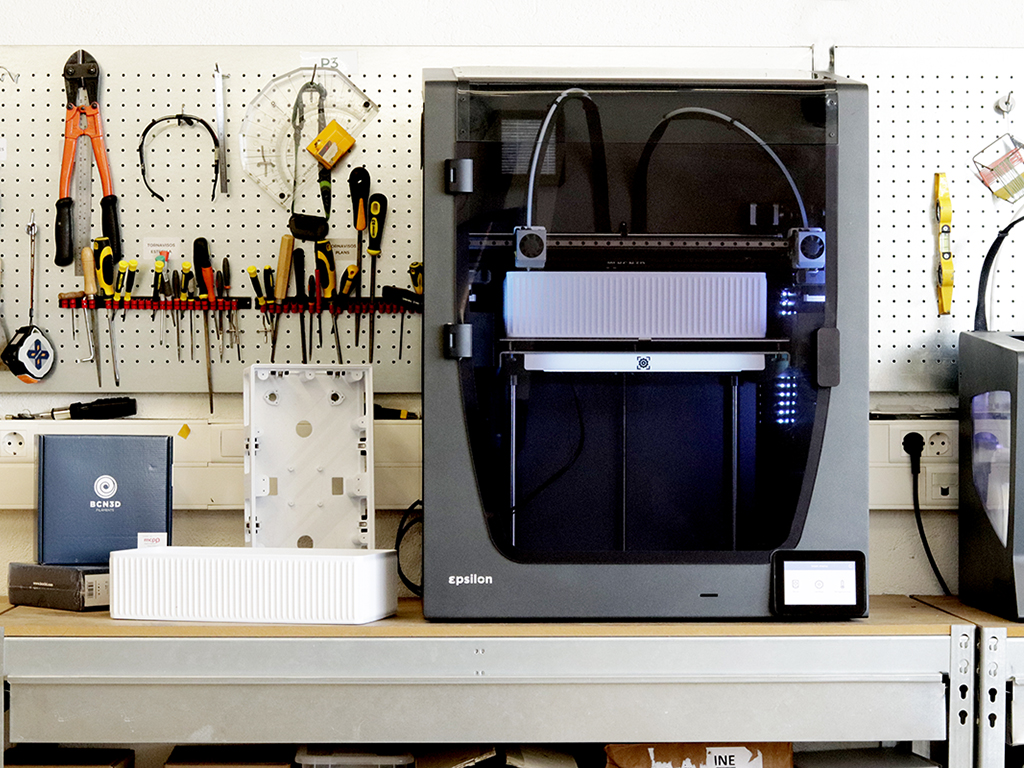
Cisco Live 2020 shows 3D printing enables agility and fuels innovation
Relying on 3D printing to fabricate their installation for the Cisco Live 2020 event yielded remarkable cost savings for Domestic Data Streamers, while enabling this creative studio to design, produce and set up fully their unique Recommendation Wall in the astonishing period of only 4 weeks.
Learn moreDlimit: iterating to perfection thanks to 3D printing
Dlimit has revolutionized its workflow since incorporating 3D printing for functional validation on their product design process. This technology has enabled them to create many iterations of each part at a low cost, ensuring to always achieve the desired result when it comes to the development of their queue management systems.
Learn more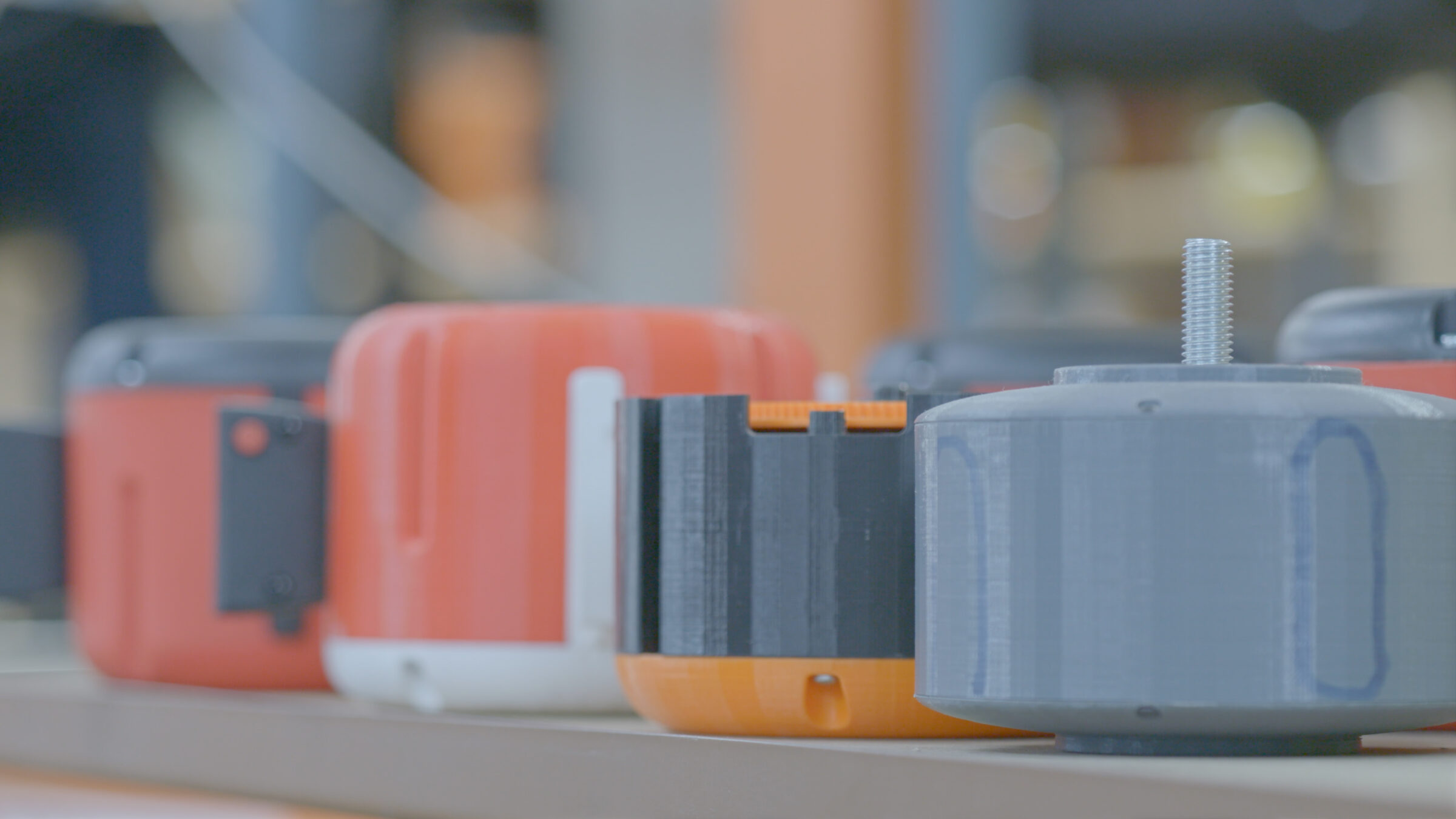
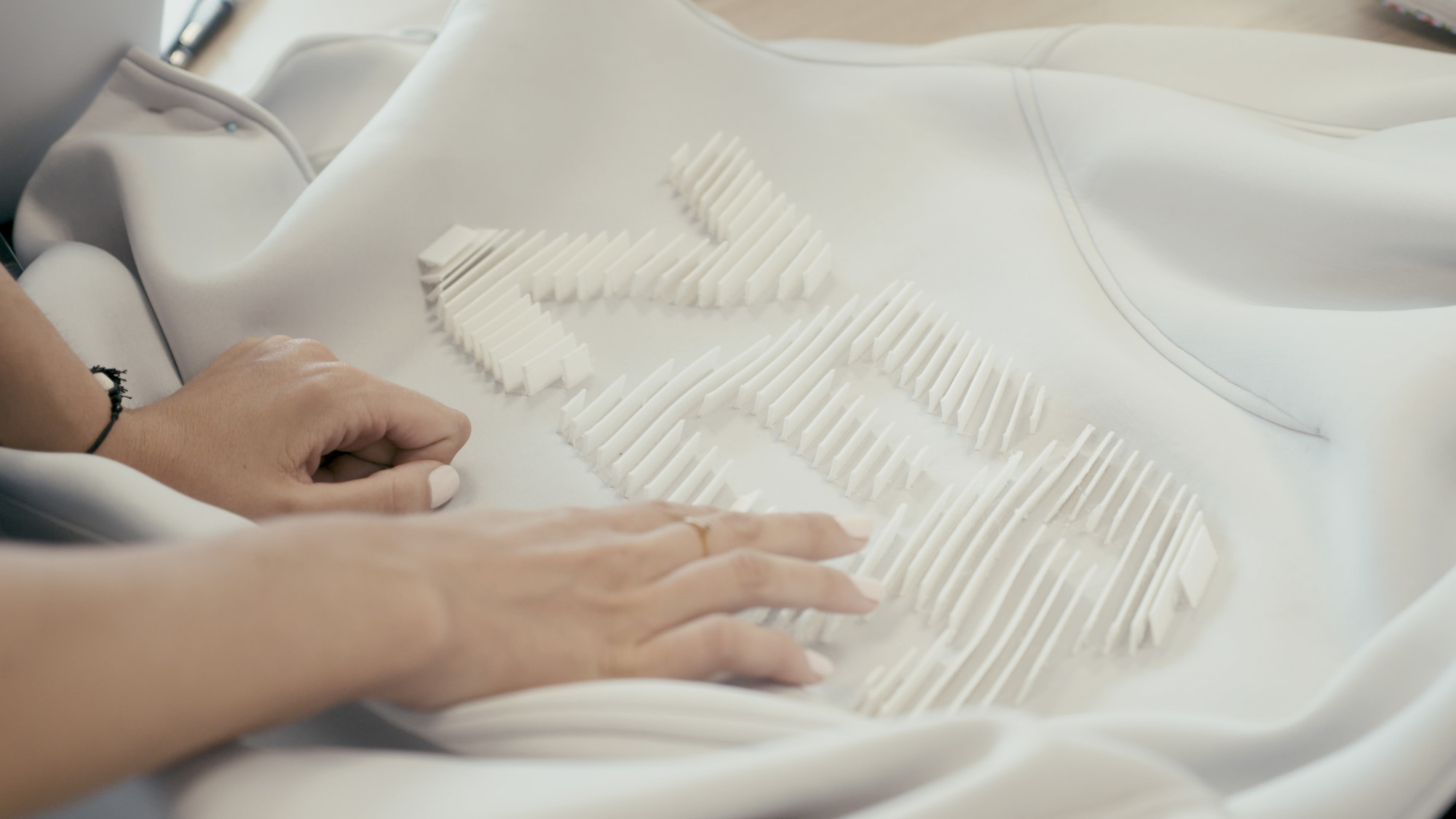
The future of fashion can be worn today: ZER Collection unites style and sustainability through 3D printing
Young brand ZER Collection has revolutionized the Spanish fashion scene by incorporating 3D printing into its designs with a double goal: to accelerate production processes, and to bet on sustainability through the reduction of waste and the use of recycled materials.
Learn moreCamper: revolutionizing the design process for footwear through in-house 3D printing
Developing tangible models in-house through 3D printing has significantly accelerated the process of launching a new collection for the Spanish-based shoe company, while yielding considerable cost savings along the way.
Learn more
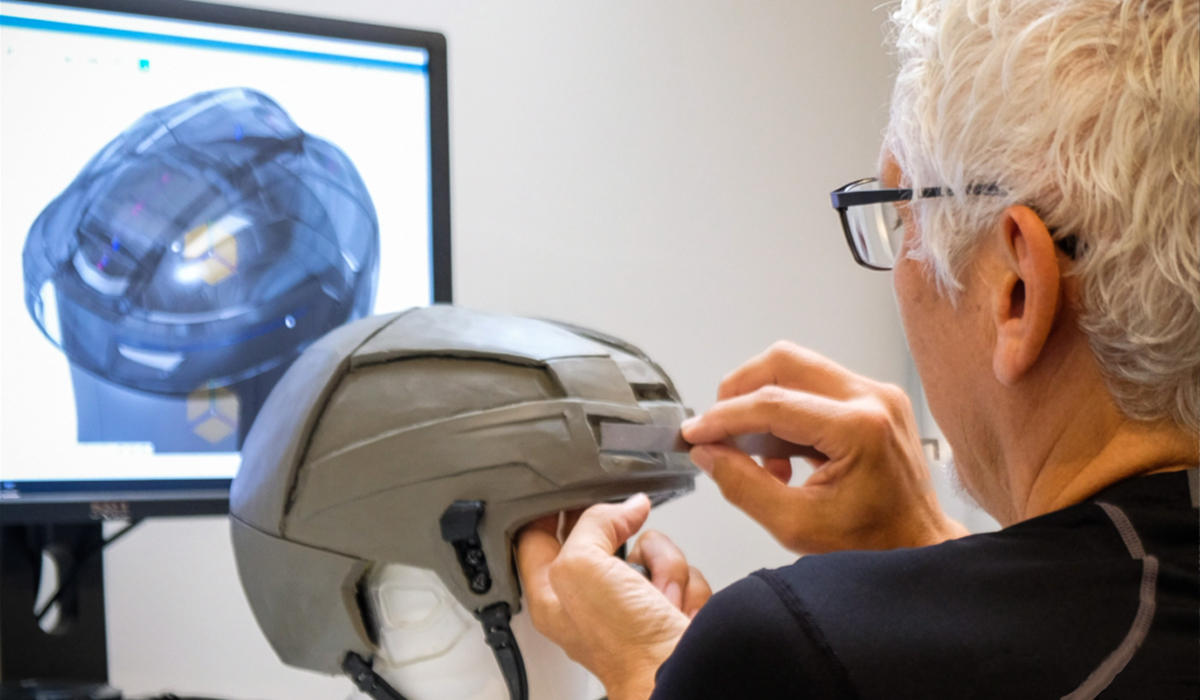
KAV is Bringing Bespoke Helmets to the Masses
Every year there are 3.8 million concussions from athletic endeavors. However, the six on the hockey team of Whitman Kwok’s son are what compelled the creation of KAV.
Learn moreBORN Motor: 3D printed motorcycle parts for time and cost savings
BORN Motor customizes high-quality deconstructed motorcycles and is using 3D printing for manufacturing final parts instead of traditional processes, saving €2,000 for each motorcycle modified.
Learn more
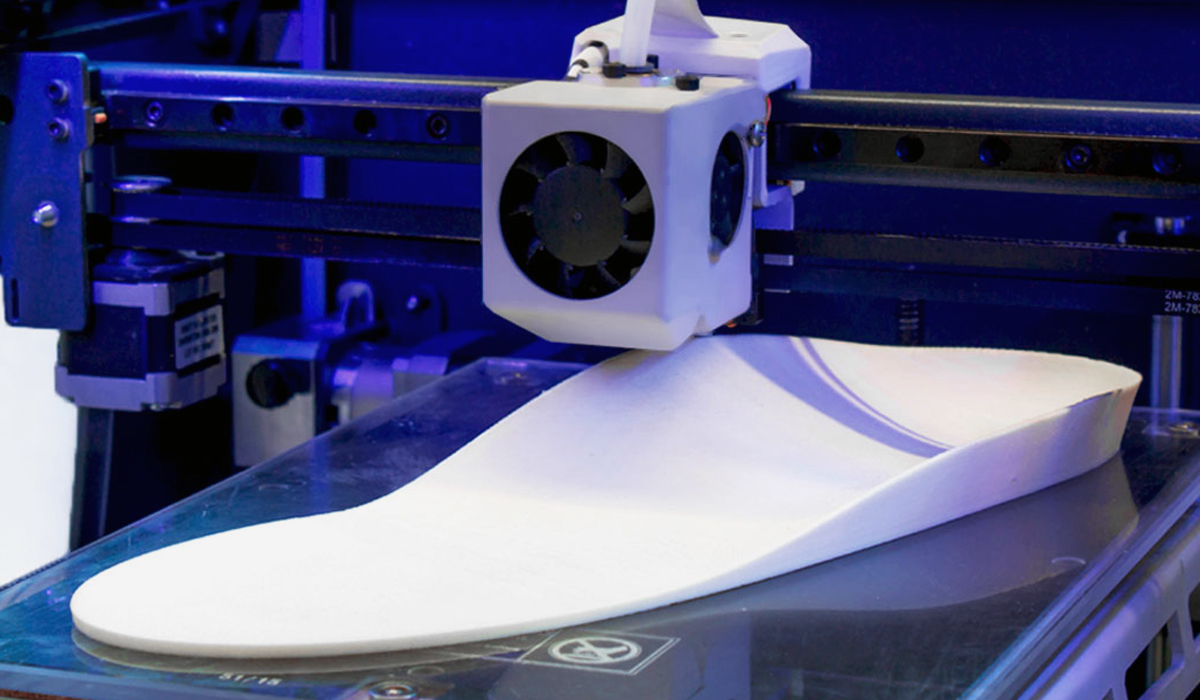
Zoles company manufactures custom 3D printed insoles drastically reducing costs and shrinking lead times
Zoles manufactures customized insoles around Europe using BCN3D printers, speeding up all the process and being able to save up to 80% of the total production costs with each pair.
Learn more