The BCN3D Sigmax revolutionizes ETSEIB Motorsport’s workflow
ETSEIB Motorsport is one of the most experienced teams in the Student Formula competition. Thanks to their BCN3D Sigmax 3D printer, they have sped up their design process, fabricated end-use pieces, and reduced time and costs.

The ETSEIB Motorsport team is made up of 40 industrial engineers from the Polytechnic University of Catalonia. After making combustion cars for 4 years and electric cars for the past 6, this is the 10th consecutive year that they have designed a formula vehicle.
The Student Formula is a competition between students from universities around the world that promotes excellence in engineering. Team members design, build, test, and race a formula style racing car. This year, the ETSEIB Motorsport team is competing using their BCN3D Sigmax printer and the benefits that have come along with it.
Ways 3D printing enhanced the workflow
Since the ETSEIB Motorsport has incorporated 3D printing FFF desktop technology into their day-to-day operations, their design and fabrication processes have drastically improved. Additive manufacturing has served them well in three main areas:
· Improvement in the design validation stage:
Having a 3D printer in-house allows the engineers to print their CAD designs overnight, significantly reducing the validation and iteration time. This new procedure ensures the Formula team no longer depends on external suppliers to fabricate their parts, allowing them to spend more time developing new ideas and concepts.
· Rapid manufacturing of cost-effective end-use parts:
Secondly, 3D printing has helped them to manufacture parts that are directly mounted on the car itself, such brake ducts, several cable ties and even molds for carbon fiber pieces. Thanks to the BCN3D Sigmax 3D printer, the ETSEIB Motorsport team has been able to optimize their production and achieve greater efficiency.
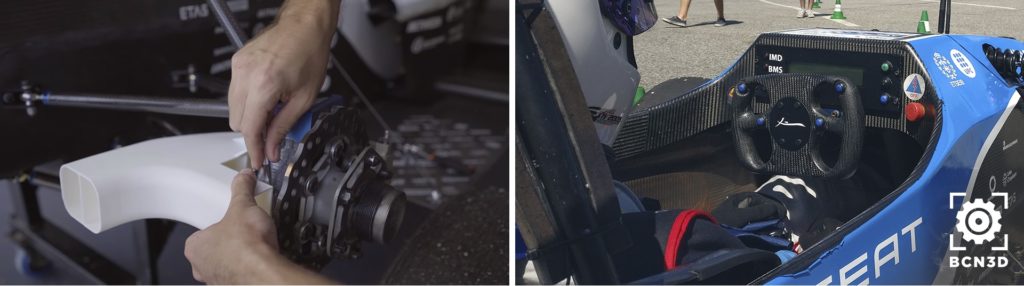
· Reducing car cost and shrinking lead times:
Finally, desktop in-house 3D printing has cut the costs of the car. The team has been able to produce parts quicker and at a lower cost than using traditional fabrication methods, especially in the design of unique and complex pieces. By using the BCN3D Sigmax 3D printer, the team has saved thousands of euros in the car development. The initial investment was fully paid back during the first months of usage.
The power of the BCN3D Sigmax
The team at ETSEIB Motorsport chose the BCN3D Sigmax 3D printer for its massive printing volume, which allowed them to easily place certain parts of the car on the printing platform.
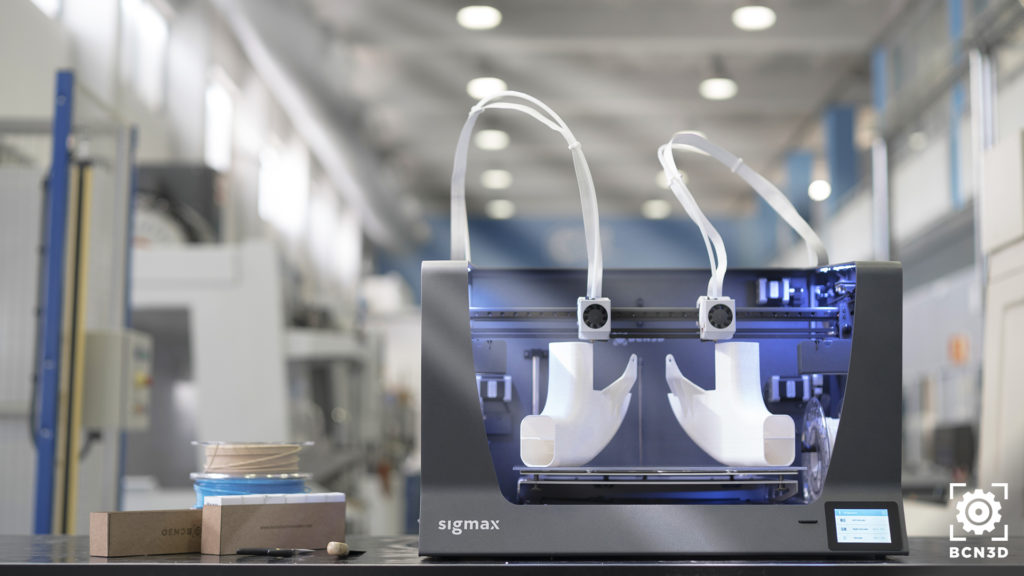
Furthermore, with the Independent Dual Extruder (IDEX) system and mirror mode, the engineers are able to print symmetrical pieces at the same time. This is of great use in the automotive field since many of the pieces are symmetrical.
Our series of hotends has allowed them to choose a hotend suitable for each moment. For small parts that need a lot of precision, they used Ø0.4 mm size nozzles. However, for larger pieces that are going to be subjected to mechanical stress, they used bigger nozzles such as Ø0.8mm or Ø1.0mm.
By using 3D printing technologies, ETSEIB Motorsport is able to fabricate parts for formula-type cars quickly and affordably. Are you interested to find out what BCN3D Technologies can do for your business? Contact us at info@bcn3dtechnologies.com, we love hearing from you!